Porosity in Welding: Identifying Common Issues and Implementing Ideal Practices for Avoidance
Porosity in welding is a prevalent issue that frequently goes undetected up until it causes significant issues with the stability of welds. In this discussion, we will certainly check out the vital aspects contributing to porosity formation, analyze its destructive impacts on weld performance, and go over the finest practices that can be taken on to decrease porosity occurrence in welding processes.
Usual Reasons of Porosity
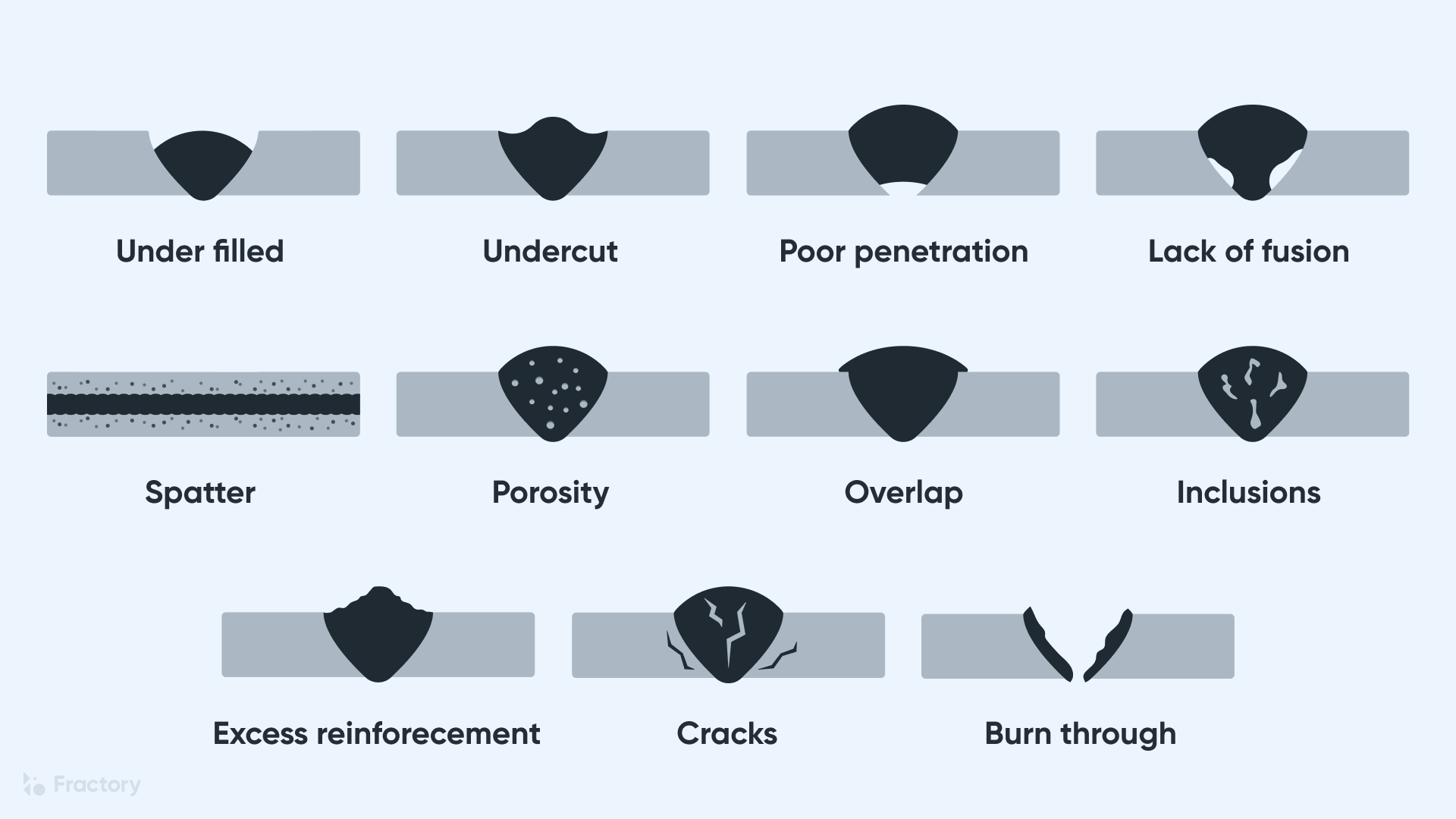
One more constant wrongdoer behind porosity is the presence of contaminants externally of the base metal, such as oil, grease, or corrosion. When these impurities are not properly gotten rid of prior to welding, they can evaporate and become entraped in the weld, creating defects. Additionally, making use of filthy or damp filler products can present impurities right into the weld, adding to porosity issues. To alleviate these common reasons for porosity, detailed cleansing of base metals, proper shielding gas selection, and adherence to ideal welding parameters are vital techniques in attaining high-grade, porosity-free welds.
Effect of Porosity on Weld Quality

The visibility of porosity in welding can substantially compromise the structural stability and mechanical buildings of bonded joints. Porosity creates gaps within the weld metal, compromising its total toughness and load-bearing ability. These gaps serve as stress and anxiety focus points, making the weld much more susceptible to breaking and failing under used lots. Furthermore, porosity can decrease the weld's resistance to corrosion and other environmental aspects, additionally decreasing its durability and performance.
Among the key repercussions of porosity is a reduction in the weld's ductility and durability. Welds with high porosity degrees often tend to display lower influence strength and minimized capacity to deform plastically before fracturing. This can be especially worrying in applications where the welded parts go through dynamic or cyclic loading conditions. Moreover, porosity can hinder the weld's ability to efficiently transmit forces, bring about premature weld failing and prospective safety and security hazards in critical frameworks.
Best Practices for Porosity Prevention
To improve the architectural stability and quality of welded joints, what specific actions can be carried out to minimize the event of porosity throughout the welding process? Making use of the correct welding Going Here technique for the details material being welded, such as changing the welding angle and gun placement, can additionally avoid porosity. Routine examination of welds and prompt remediation of any kind of concerns recognized throughout the welding process are necessary techniques to avoid porosity and create high-grade welds.
Significance of Correct Welding Strategies
Implementing proper welding methods is paramount in ensuring the structural integrity and quality of bonded joints, constructing upon the foundation of efficient porosity prevention steps. Excessive warmth can lead to enhanced porosity due to the entrapment of gases in the weld pool. Furthermore, using reference the suitable welding specifications, such as voltage, current, and take a trip rate, is critical for accomplishing audio welds with very little porosity.
Moreover, the option of welding process, whether it be MIG, TIG, or stick welding, ought to align with the details needs of the job to ensure ideal outcomes. Proper cleaning and preparation of the base metal, as well as choosing the right filler product, are also important elements of competent welding methods. By adhering to these finest techniques, welders can reduce the risk of porosity formation and create top quality, structurally sound welds.

Checking and High Quality Control Steps
Examining procedures are crucial to spot and stop porosity in welding, ensuring the toughness and sturdiness of the final product. Non-destructive testing techniques such as ultrasonic screening, radiographic testing, and visual examination are generally utilized to determine you could try here prospective issues like porosity.
Carrying out pre-weld and post-weld assessments is likewise vital in keeping quality assurance standards. Pre-weld inspections include verifying the products, devices setups, and sanitation of the workspace to stop contamination. Post-weld inspections, on the other hand, analyze the final weld for any type of issues, consisting of porosity, and confirm that it meets specified criteria. Carrying out a detailed quality assurance strategy that includes complete screening procedures and evaluations is vital to decreasing porosity problems and making certain the overall top quality of welded joints.
Verdict
Finally, porosity in welding can be a common issue that influences the high quality of welds. By recognizing the usual sources of porosity and executing finest methods for avoidance, such as correct welding techniques and testing measures, welders can make certain high quality and reliable welds. It is important to prioritize avoidance methods to minimize the event of porosity and keep the stability of bonded frameworks.